Klintek Engineers are specialists in gravity die casting, with one of the most advanced facilities in the indian foundry industry.
Aluminum gravity die casting is a highly popular and widely used casting process in which molten aluminum is poured into a permanent metal mold or die. The molten metal solidifies inside the mold under gravity and is then ejected from the mold, resulting in a high-quality aluminum casting.
The process of aluminum gravity die casting involves several steps, including mold preparation, pouring the molten aluminum alloy, cooling, and ejection.
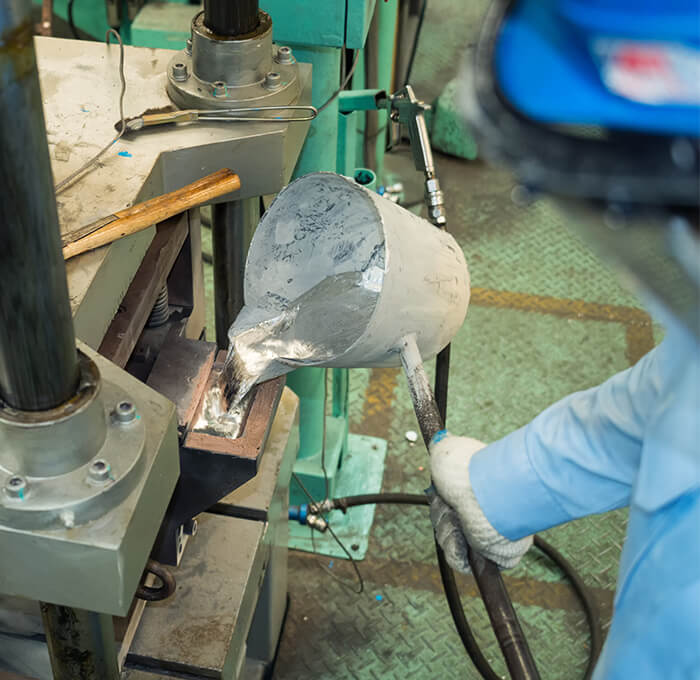
The mold is preheated to a specific temperature, and a refractory material is coated onto the mold surface to prevent the aluminum from sticking. The molten aluminum alloy is then poured into the mold cavity, and it solidifies under gravity. After the casting has cooled, the mold is opened, and the casting is ejected using a hydraulic or mechanical press.
Aluminum gravity die casting has several advantages over other casting methods, such as excellent dimensional accuracy, reduced post-casting machining, and cost-effectiveness. The process is ideal for producing high-quality, intricate, and complex parts made of aluminum alloys that have a smooth surface finish and minimal porosity. The equipment used in aluminum gravity die casting includes a mold or die made of steel or iron, a furnace to melt the aluminum alloy, a ladle to transfer the molten aluminum to the mold, and a cooling system to cool the mold and casting after pouring.
Several types of aluminum alloys are used in gravity die casting, including A356, A380, and ADC12. These alloys have different properties, such as high strength, ductility, corrosion resistance, and thermal conductivity, and are used in various applications in the automotive, aerospace, and industrial manufacturing industries.
Different aluminum die casting processes have different molds and hence have varying service lives. To maintain the functionality of the die cast mold, it is important to increase its service life. It can be done during the production of the mold and sometimes regulations are required during its service life to maintain its efficiency. If the maintenance is not carried out, it might affect the uniformity of the die casted parts.
Klintek Engineers has optimised the productivity of its gravity die casting processes
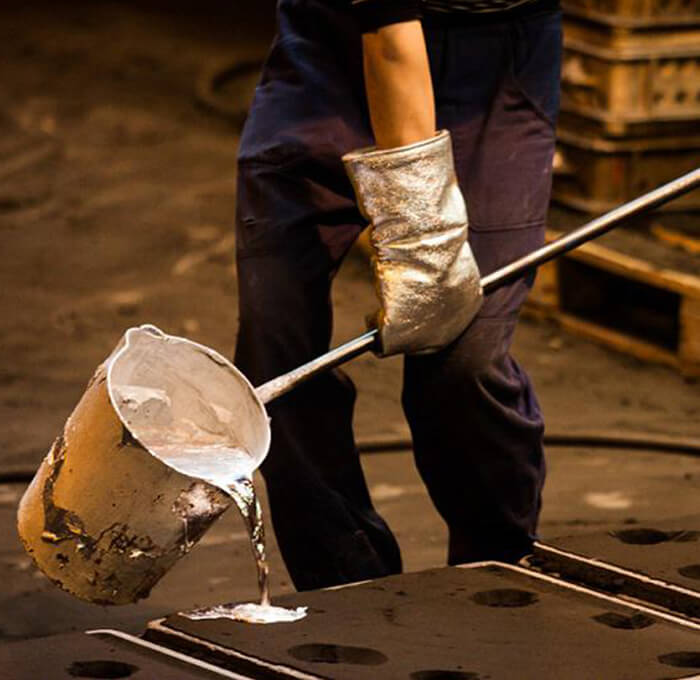
Klintek Engineers are premier global sand casting manufacturer that offers a wide range of high-quality metal casting services.
Aluminium sand casting is a process used to create metal components by pouring molten aluminium into a sand mold. The process involves several key steps, including pattern making, mold making, pouring, cooling, and finishing.
The first step in the process is pattern making, which involves creating a replica of the final product that will be cast in metal.
The pattern is typically made from wood, plastic, or metal, and is slightly larger than the final product to account for shrinkage during the cooling process.
The next step is mold making, which involves packing sand around the pattern in a box called a flask. The sand used in the process is a special type of sand called foundry sand, which is mixed with a binder to hold the sand together and create a solid mold.
Once the mold is made, the molten aluminium is poured into the mold through a gate. The temperature of the molten aluminium is carefully controlled to ensure that it is the correct temperature for pouring and to avoid defects in the finished product.
After the molten aluminium is poured into the mold, it is allowed to cool and solidify. The cooling time depends on the size and shape of the component being cast. Once the metal has solidified, the mold is opened, and the casting is removed.
The final step in the process is finishing, which involves removing any excess material and cleaning and polishing the casting to give it the desired finish.
Aluminium sand casting is a cost-effective way to produce large quantities of metal components. The process is also flexible, allowing for a wide range of shapes and sizes to be produced. The sand used in the process is readily available and easy to work with, and the molds can be reused multiple times.
If you are looking for a reliable and cost-effective way to produce metal components, aluminium sand casting may be the ideal solution for your needs.
Why use Klintek Engineers Sand Casting?
Let’s Get to Work On Your Project
There are many different metal casting methods. At Precise Cast, we have chosen two aluminum casting methods that are especially well suited to low-volume production.
Contact Us